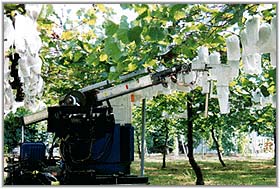
Fig.1 Multi-operation robot for grapevine (Bagging operation).
(MPEG4、14MB)
|
Fig.1 shows a robot to work in vineyard (Kondo, 1995f). In open field, harvesting period is so short that a harvesting robot may not be efficient if it is not able to do other operation. To make working period of the robot longer, several end-effectors were developed (Kondo et al., 1996d, Monta et al., 1995a).
|
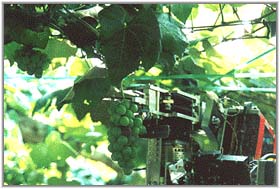
Fig.2 Harvesting end-effector.
(MPEG1、1.7MB)
|
This robot has a polar coordinate manipulator with five degrees of freedom. The manipulator end could be moved on horizontal plane below the trellis at a constant speed under CP control. The length of the arm was 1.6 m, and the stroke was 1 m. In our laboratory, a harvesting end-effector (Fig.2), a berry thinning end-effector, a bagging end-effector, and a spray nozzle were attached to the manipulator end and experimented. This robot was a larger than the tomato harvesting robot and its mass was about 200kg. A crawler type traveling device was prepared for mounting the robot.
|